Defects In Quality- An Important Aspect That Can’t Be Ignored
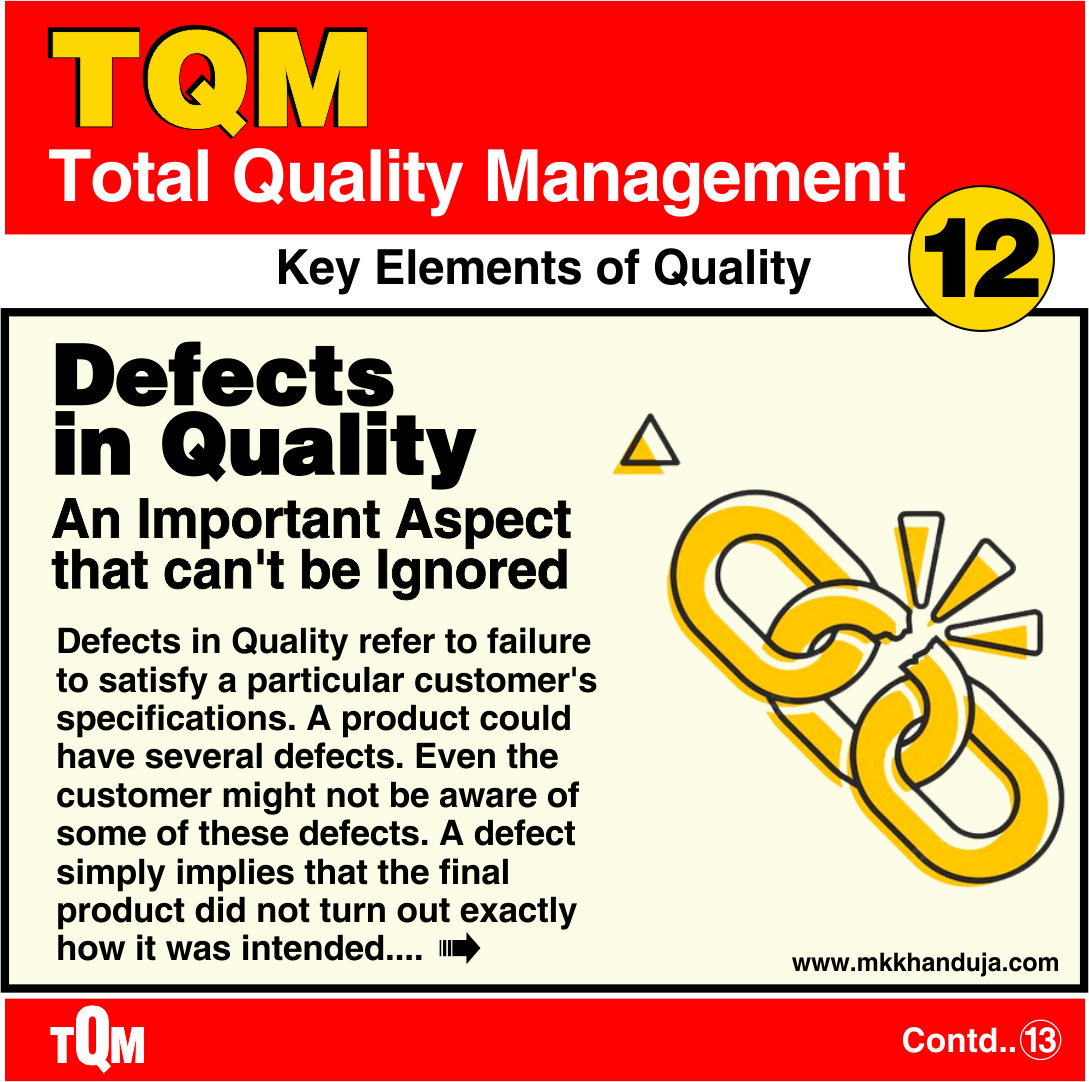
Defects in Quality refer to failure to
satisfy a particular customer's specifications. A product could have several
defects. Even the customer might not be aware of some of these defects. A
defect simply implies that the final product did not turn out exactly how it
was intended.
Understanding Defects
Defects are inevitable in any
manufacturing process. What is important is how to identify and address them.
The quality process involves identifying defects and then taking steps to
eliminate or minimize them. The first step is to identify the root cause of the
defect. Once the root cause is identified, steps can be taken to prevent it
from happening again.
How To Manage Process Defects?
Defects can be reduced or minimized as they
result in the wastage of resources in the form of scrap, labor, energy
consumption, materials, etc. These are called “internal failure costs”. A
company may have external failure costs such as warranty, recall, and
reputational damage if a defective product is shipped to the customer. These
expenses might necessitate a price reduction and result in losses.
Important Metrics to Monitor Defects
Different metrics can be used to help manage defects. Let us discuss some of the most important ones:1. Defects per Unit (DPU):
This metric is used to calculate the average number of defects per unit. It is
important to track this number to identify trends and problem areas.
2. Defects per Million
Opportunities (DPMO): This metric is used to calculate the number of defects
per million opportunities. It is a good way to measure the severity of defects
and track improvement over time.
3. Defect Removal Efficiency
(DRE): This metric is used to calculate the percentage of defects that are
identified and removed before they reach the customer. A high DRE indicates
that the quality assurance process is working well.
4. Yield: This formula is
used to calculate the number of good units out of the total number of units
produced. It is a good way to measure the overall quality of the product.
5. Cost of Quality (COQ):
This method is used to calculate the
total cost of quality, including the cost of prevention, appraisal, and
failure. It is a good way to measure the financial impact of defects.
Tracking through these
important methods will help in managing defects effectively & improve the
quality of the product.
Managing Defects Effectively
Defects can be managed
effectively through standardization and continuous improvement of resources.
Here are some ways to manage defects:
1. Preventing defects from
occurring in the first place. This can be done through effective quality
control measures such as inspection and testing.
2. If defects do occur, it is
important to identify them as quickly as possible. This can be done through
inspection, testing, and customer feedback.
3. Once defects are
identified, necessary steps can be taken to fix them. This can be done through
re-inspection, re-testing, and repair or replacement.
4. Preventing the recurrence
of defects. This can be done through process improvement measures such as
process redesign and implementation of better quality control measures.
Key Takeaways
- The term “non-conformity” is used to signify Defect.
- A defect indicates that only the product result is not entirely as intended.
- A defect is any item or product that exhibits a departure from its specifications.
- A defect does not necessarily mean that the product cannot be used.
- Defects are subsets of defective.
Comments