Variation The Enemy No. 1 of Quality
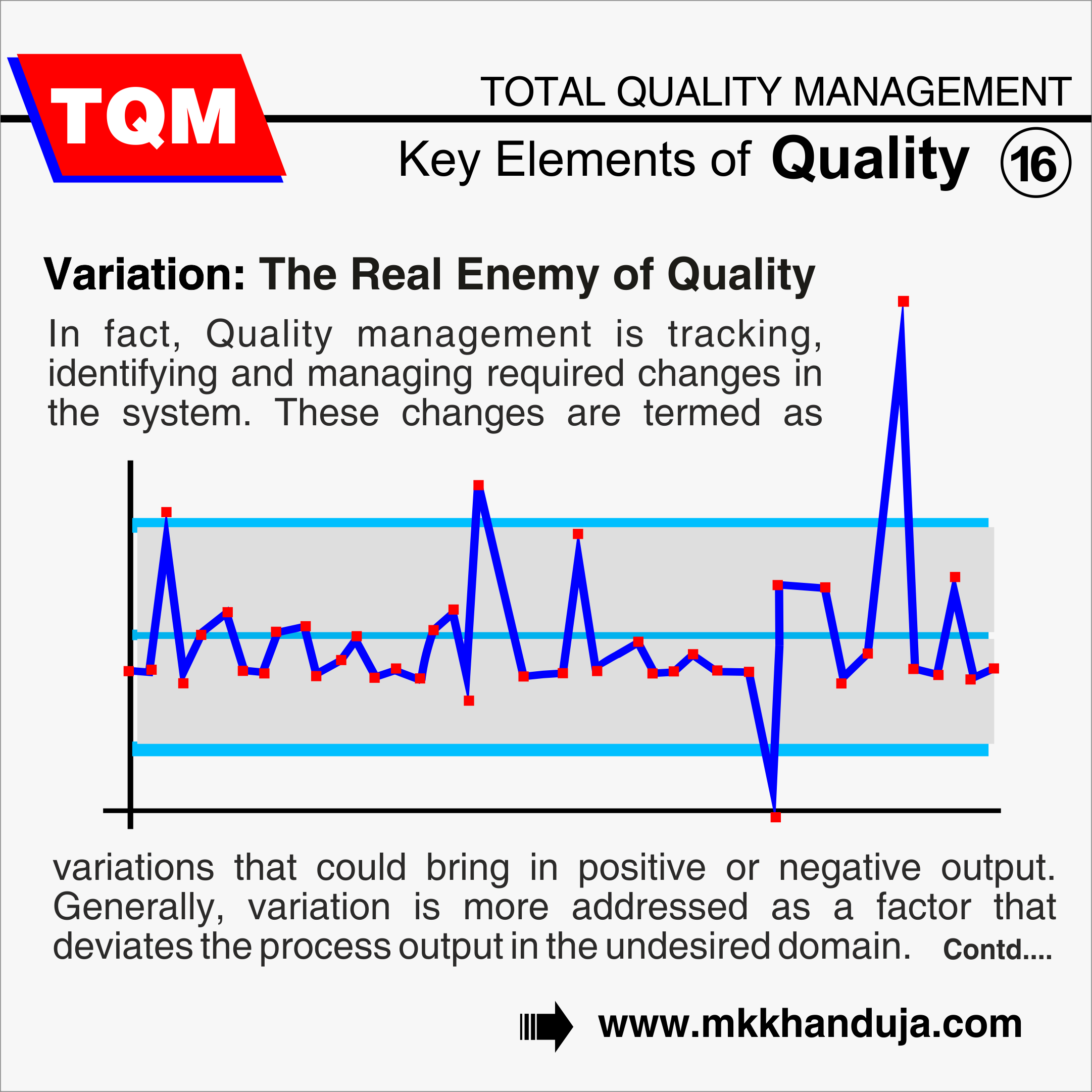
Variation – The Enemy No.1 of Quality
In fact, Quality management is tracking, identifying and managing required changes in the system. These changes are termed as variations that could bring in positive or negative output. Generally, variation is more addressed as a factor that deviates the process output in the undesired domain. The variation can lead to huge customer dissatisfaction.
Examples
- 20% Customer calls getting disconnected at call centre.
- 10% Biscuits broken in the packet.
- Variation in component dimensions after machining.
In Quality system the desired output is defined by customers or stakeholders, as product specifications. This is also called ‘Voice of Customers’ (VOC) in six sigma methodology. A good quality system in business always try to meet the customer’s expectations (VOC) by delivering what exactly is needed. This is made feasible by utilising appropriate resources being transformed into desired output (VOC) following appropriate processes religiously. This leads to minimum variation in the process.
Type of Variation
A. Common cause variation
Some degree of variation naturally occurs in any process. This is an individual characteristic of a process. To minimise this kind of variation, It needs a very detailed process study and structured intervention. This is a long-term initiative. This can bring in holistic change but it needs a very matured and professional intervention.
B. Special cause variation
This variation is not the intrinsic part of process. This happens due to unexpected occurrence. This is important identify and eliminate such variation as soon as possible in the system.
Control Chart – This is visual depiction of variation. Control Chart is the graphical representation of any process in the system, depicting common and special cause variations. One can draw important decisions by observing trends depicted in control chart.
Comments