Method PPAP Production Part Approval Process
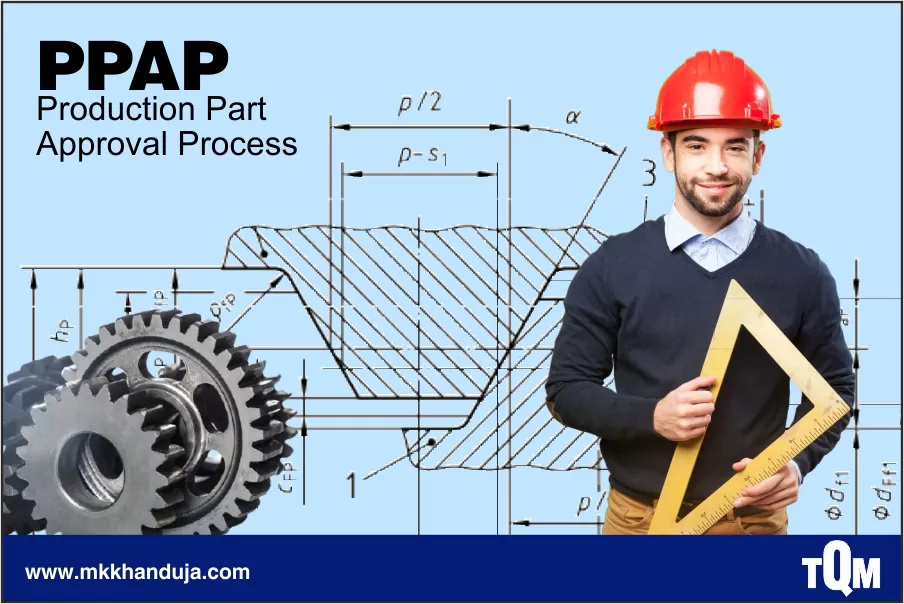
TQM Method of PPAP is a holistic approach that builds conviction in suppliers and their processes
When the need was felt to standardize the process of manufacturing and material quality, PPAP took the shape. It can be defined as a quality tool that helps an organization to build conviction in its suppliers and their manufacturing processes. Nowadays Production Part Approval Process (PPAP) has become one of the finest ways to ensure the high-quality standards of a product supplied, and its manufacturing process. The Automotive Industry Action Group (AIAG) developed the most systematic way of PPAP in 1993 to assure the product should be delivered as per the client's requirements.
Before Pwas not standardized. After introducing PPAP, the standardized quality processes were created and the PAP, everyone has their own quality standards and they were neither competitive nor comparable to each other. Everything was scattered and making the right judgement towards quality PPAP submission requirements were categorized in below five levels.
Level 1. Only Part Submission Warrant (PSW) submitted to the customer.
Level 2. The PSW is submitted with product samples along with limited supporting data.
Level 3. The PSW is submitted with product samples along with complete supporting data.
Level 4. PSW along with other requirements are submitted as defined by the customer.
Level 5. PSW with product samples and the complete supporting data to made available for review at the supplier's manufacturing location.
Adopting this process of TQM ensures good quality products along with higher productivity and efficiency.
Comments