3 Continuous Improvement Tools That Empower The Effective TQM Implementation
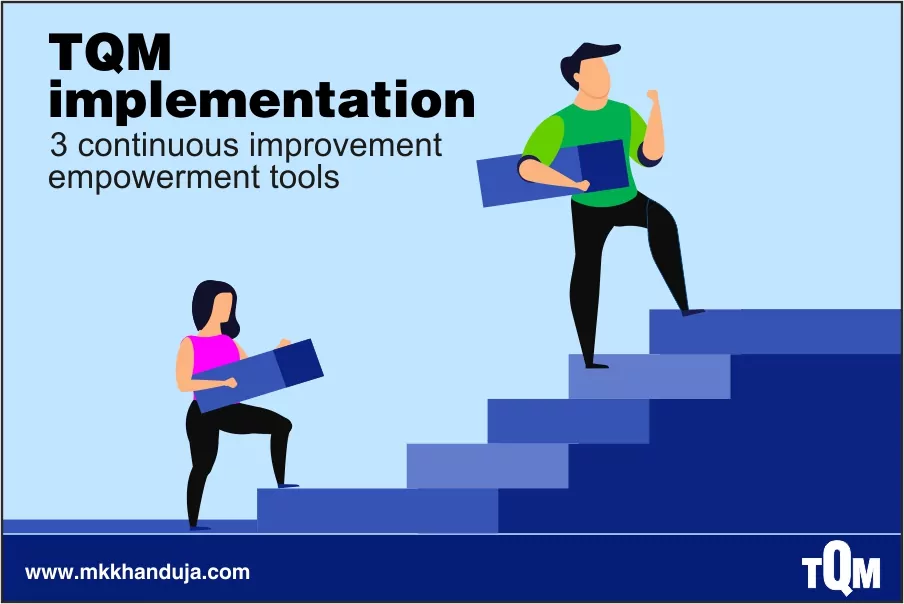
An organization spends time & effort in total quality management just to achieve customer satisfaction. The ideal goal of TQM – doing things right, the first time, and every time, depends on how an organization is leveraging the continuous improvement tools and techniques. Here are the three core continuous improvement tools to get you the powerful results from TQM.
1. Process Mapping - Process mapping is the first step in the continuous improvement process while implementing the TQM strategy. It involves an accurate understanding of the process that needs improvement. The prerequisite of continuous improvement is that the process should be mapped to identify the process flow quickly.
For example, in a manufacturing process, the mapping involves purchasing goods from vendors until providing customer service to the consumers. Process mapping is the graphical representation of the process from start to finish, including a set of activities and the outcomes.
2. Root Cause Analysis - The RCA is a method in which an organization finds the root cause of quality concerns or any other problem. It has three phases.
• Open Phase: It is an initial phase where the participants brainstorm to find the possible root causes of a problem. The 5 Why's the analysis and fishbone diagram (cause and effect analysis) are the best tools for brainstorming sessions.
During this process, the teams try to identify the possible causes in different categories such as workforce, materials, methods, machines, and measurements.
• Narrow Phase: In this phase, the team narrows down the possible root causes and focuses on the most significant possibilities.
• Closed Phase: This is the last stage of the RCA process, where the team reaches the final root cause after thorough validation and is based on evidence. Several methods are used, such as the scatterplot diagram, Pareto charts, and the check sheets to determine an event's frequency.
3. PDCA Cycle (Plan-Do-Check-Act) - PDCA cycle consists of four phases to carry out the change. These are:
• Plan: This is a planning phase that begins after identifying the root cause of a problem or quality concern. It includes creating an improvement strategy for the improvement process.
• Do: this stage includes to take action as per the planning stage and to implement a change.
• Check: This phase is used to validate that the changes are producing the desired results. If it doesn't, then you will have to restart the PDCA cycle again.
Comments